Blog
Frequently Asked Questions (FAQ) on Freeform Injection Molding (FIM)
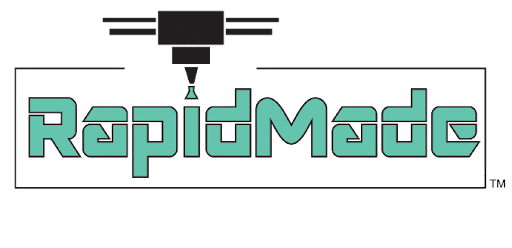
General Questions
- What is Freeform Injection Molding (FIM)?
Freeform Injection Molding (FIM) is a manufacturing process that utilizes 3D-printed molds instead of traditional metal tooling, enabling rapid prototyping and complex part geometries.
- How does FIM differ from conventional injection molding?
Unlike conventional injection molding, which requires expensive and time-consuming machined metal molds, FIM uses 3D-printed molds for faster iteration and lower production costs.
- What are the benefits of using FIM?
FIM allows for rapid prototyping, reduced tooling costs, and the ability to create complex geometries that would be difficult with traditional molding methods.
- What are the limitations of FIM?
3D-printed molds may have lower durability than metal molds, limiting their lifespan. Additionally, material compatibility and heat resistance must be carefully considered.
- What industries benefit most from FIM?
Industries such as medical device manufacturing, automotive prototyping, consumer goods, and aerospace benefit from FIM due to its ability to produce complex and customized parts quickly.
Mold Design and Printability
- What factors affect the printability of an FIM mold?
Key factors include wall thickness, overhangs, bridging, print orientation, and mold surface details, all of which impact structural integrity and accuracy.
- What is the recommended wall thickness for 3D-printed molds?
Supported walls should be at least 1 mm for small features, 2 mm for load-bearing areas, and 3 mm for high-stress regions. Unsupported walls should be at least 0.8 mm thick.
- How can I prevent warping in unsupported mold sections?
Warping can be minimized by maintaining proper thickness, reinforcing walls with fillets or ribs, and limiting aspect ratios to 5:1.
- Why is print orientation important in FIM?
Proper print orientation reduces delamination, improves resolution for fine details, and minimizes the need for support structures, which simplifies post-processing.
- How should clearance be managed between mold sections?
A minimum clearance of 2 mm should be maintained between mold sections to prevent unintended fusing and ensure easy separation after molding.
- What are the minimum hole sizes that can be printed in an FIM mold?
Holes aligned with the X, Y, or Z axes should be at least 0.7 mm in diameter, while curved or angled holes should be at least 1 mm.
FOR MORE INFORMATION CLICK HERE : luxury massage dubai
Split Molds and Assembly
- What is a split mold, and why is it used in FIM?
A split mold is a multi-part mold designed to simplify demolding and allow for more complex geometries that would be difficult to produce with a single-piece mold.
- How do split molds improve print success?
By dividing a mold into multiple sections, large overhangs and unsupported features are eliminated, reducing the likelihood of print failures.
- What are the advantages of using multi-part molds?
Multi-part molds improve structural integrity, simplify cleaning, enhance curing efficiency, and allow for better venting during injection molding.
- How are split molds aligned and assembled?
Alignment is achieved using guide bars, which should be undersized by 0.03 mm for a precise fit. Bolts should be placed strategically to evenly distribute pressure.
- How does venting in split molds help the molding process?
A small gap (~0.02 mm) along the mold split acts as a natural vent, allowing air to escape and preventing defects like short shots and voids.
Injection Molding Process Optimization
- How should injection points be positioned in an FIM mold?
The injection inlet should be placed at the deepest cross-section to ensure uniform material flow, while the outlet should be positioned opposite to capture cold slugs.
- How can material flow be improved in FIM?
Proper venting, strategic inlet/outlet placement, and optimizing mold temperature settings can enhance material distribution and reduce defects.
- What are the common defects in FIM and how can they be prevented?
Common defects include warping, air entrapment, short shots, and surface imperfections, which can be prevented through proper mold design and material selection.
- What materials are compatible with 3D-printed molds in FIM?
Thermoplastics such as PLA, ABS, and TPU are commonly used, but mold material must be heat-resistant enough to withstand injection pressures.
Demolding and Surface Preparation
- How can I ensure easy mold removal after injection?
Chamfered edges, venting channels, and vacuum relief tracks can prevent suction forces and make demolding easier.
- What are the benefits of using dissolvable molds?
Dissolvable molds allow for the creation of highly intricate parts that would be difficult to demold manually. These molds break down in specific solvents, eliminating the risk of damage.
- What surface treatments can improve demolding efficiency?
Applying slip agents, incorporating grooves along split lines, and limiting dissolution time can help streamline demolding.
- How can mold wear and tear be minimized?
Ensuring proper mold thickness, reinforcing stress points, and avoiding excessive heat exposure can prolong the lifespan of 3D-printed molds.
Testing and Iteration
- Why is testing multiple mold iterations important?
Prototyping multiple designs (typically 4–8 variants) helps identify the best mold configuration for optimal performance and efficiency.
- What role does mold simulation software play in FIM?
Mold simulation software predicts material flow, cooling behavior, and potential defects, allowing engineers to optimize mold designs before printing.
- How does mold simulation improve workflow efficiency?
By detecting issues early, mold simulation reduces the number of trial-and-error iterations, saving both time and material costs.
- What are common issues detected by mold simulation?
Air entrapment, short shots, weld lines, and excessive shrinkage or warping can be identified and corrected using simulation software.
- What is the typical workflow for optimizing an FIM mold design?
The process involves creating a 3D model, running simulations, refining the design, printing and testing the mold, and iterating based on real-world performance.
- What are the key takeaways for optimizing FIM?
Ensuring proper mold printability, using split molds for complex geometries, optimizing material flow, and leveraging simulation tools are essential for producing high-quality injection-molded parts efficiently.
This FAQ provides a comprehensive guide to Freeform Injection Molding, covering design considerations, process optimization, and testing strategies. By applying these principles, manufacturers can improve mold reliability, reduce defects, and streamline production.
Looking to streamline your manufacturing process with Freeform Injection Molding (FIM)? RapidMade offers expert 3D-printed tooling solutions to accelerate production and reduce costs. Contact us today to learn how we can help optimize your mold designs and manufacturing workflow.
📩 Email: info@rapidmade.com
🌐 Visit us: www.rapidmade.com